Nano Deposition, Annealing and Etching Systems
Moorfield Nanotechnology nanoPVD, nanoCVD, MiniLab, nanoANNEAL, nanoETCH
Moorfield supplies systems for scientific research, product development and pilot/small-batch scale industrial production. Their systems are of four main types: physical vapor deposition (PVD), chemical vapor deposition (CVD), reactive ion etching (RIE) and annealing.
PVD instruments are equipped with a range of techniques including thermal and e-beam evaporation, magnetron sputtering, and ion beam sources for pre-deposition etch cleaning and IBAD (ion-beam assisted deposition). Users can create depositions of a wide range of materials including metals, dielectrics, ceramics, and organics. In addition to deposition and ion beam sources, process chambers can be fitted with hardware for in-situ rate and thickness monitoring and feedback control, load-locks, and a range of advanced stage components including heating, cooling, bias, rotation, tilt, GLAD (glancing angle deposition), gradient masking and in-vacuum mask/substrate exchange. PVD systems are available as fully customizable floor-standing units (MiniLab), or compact units suitable for benchtops (nanoPVD).
Moorfield's CVD systems were developed as compact tools for the synthesis of graphene and carbon nanotubes. Both low-pressure and atmospheric pressure tools can be supplied. Recently, the range's capabilities have been expanded to include wafer-scale production systems. Most recently, systems have been upgraded with plasma-enhanced (PECVD) capability aimed at material production at reduced temperatures.
The reactive ion etching (RIE) tools are suitable for working with sensitive films (graphene and 2D materials). While they are ideal for gentle, precisely controlled etching, the technology has now been expanded to cover more aggressive etchant gases enhancing the window of possible applications.
Annealing products offer temperatures up to 1,000° C, together with optional introduction of various process gases including with pressure control. In this way, the tools can provide full, fine control over annealing conditions as required for many research needs.
Tools can be adapted to work within glovebox environments.
Solutions
- Physical vapor deposition
- Chemical vapor deposition
- Magnetron sputtering
- Nanoparticle vacuum deposition
- Plasma etching
- Thermal evaporation
- Low temperature evaporation
- E-beam evaporation
- Glovebox integration
Models
nanoPVD
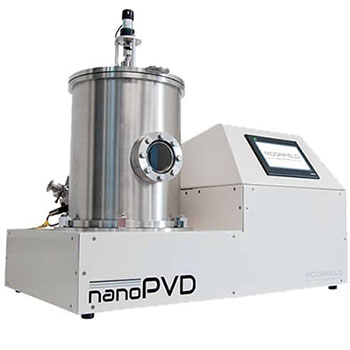
High-performance, high-vacuum PVD systems in a compact package for benchtop location. Can be equipped for evaporation or magnetron sputtering techniques and, most recently, a combination of both. Superior, efficient performance for a multitude of R&D thin-film deposition applications. Compact and suitable for benchtop location—but not to be confused with microscopy-related products—nanoPVD system design is derived from proven R&D thin-film system technology.
Moorfield's nanoPVD tools are optimized for ease-of-use, represent outstanding value for money, and are ideal where available space and budgets are key considerations—without compromising on quality of results.
FEATURES
- Benchtop configuration
- Fully automatic operation via touchscreen HMI
- Define/save multiple process recipes
- Base pressures <5 × 10-7 mbar
- Heating, Z-shift and rotation stages (optional)
- Cleanroom compatible
- Outstanding value for money
Models include: nanoPVD-S10A, nanoPVD-S10A-WA, nanoPVD-ST15A, and nanoPVD-T15A.
nanoCVD
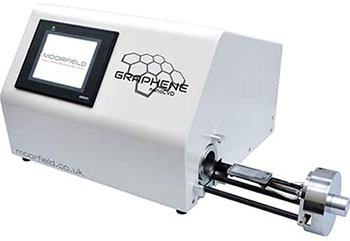
The nanoCVD range from Moorfield are compact, benchtop tools providing rapid, high-quality production of graphene or carbon nanotubes (CNTs), ideal for research groups focused on carbon nanomaterial applications who need a reliable source of on-demand samples. The systems are based on cold-wall designs associated with key benefits in comparison to hot-wall (tube furnace) counterparts:
- Rapid heating to synthesis temperatures, and cooling
- Enhanced conditions control and process reproducibility
- Low-contamination operation
- Reduced resource usage and low running costs
- Compact tools for straightforward location
All nanoCVD systems are easy to connect, quick to install and are backed-up by expert support. Touchscreen HMIs provide for recipe-based, multi-stage process control covering all crucial conditions.
FEATURES
- Ultra-compact, benchtop, CVD system
- Reproducible synthesis of high-quality graphene
- Precise control of conditions
- 1100 °C maximum temperature
- Process times <30 minutes
- 20 × 40 mm2 maximum substrate size
- Fully automatic
- User-friendly, touchscreen HMI operation
- Define/save multiple growth recipes
- Cleanroom compatible
Models include: nanoCVD-8G and nanoCVD-WG(P).
MiniLab
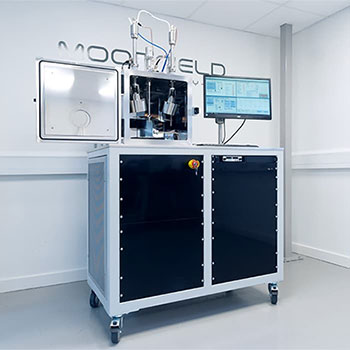
The MiniLab range from Moorfield are flexible, modular PVD systems for high-quality R&D and pilot-scale production. The tools are highly customizable and highly adaptable to suit your needs. Contact us to discuss your requirements.
- Compact, floor-standing tools
- Thermal evaporation
- Low-temperature evaporation
- Electron-beam evaporation
- Magnetron sputtering
Models include: MiniLab 026, MiniLab 060, MiniLab 080, MiniLab 090, and MiniLab 125
nanoANNEAL
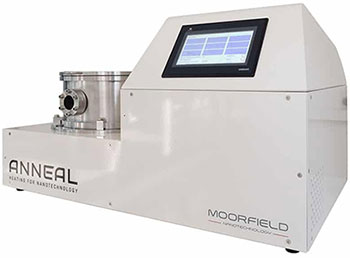
ANNEAL vacuum annealing systems from Moorfield are optimized for the thermal treatment of 2D materials and wafers under controlled atmospheres. Substrates are supported face-up on stage-top platens that are situated centrally inside a stainless-steel high-vacuum chamber fitted with appropriate heat shielding and a shuttered viewport. Heating is via a heat source located beneath the platen. Maximum temperatures up to 1000 °C are possible depending on the heating technology used:
- Quartz lamp: This technology uses quartz lamps to generate IR radiation. A cost-effective means of heating for substrate temperatures up to 600 °C, and compatible with most atmospheres. Maximum Ramp of 0.3°C/s.
- Carbon-carbon composite (CCC): Where substrate temperatures above 500 °C are required, CCC elements are used where non-oxygen compatible atmospheres are present.
- Suitable for heating up to 1000 °C. Maximum Ramp of 8°C/s.
- SiC-coated graphite: When high temperatures and oxygen resistance are required, graphite elements are coated with a resistant layer of SiC.
- Maximum Ramp of 8°C/s. Heating control resolution is to ±1 °C .
For annealing under controlled atmospheres, ANNEAL systems can be fitted with up to 3 mass flow controllers (MFCs). Typical gases are Ar, O2 and N2, and full-scale flow rates are flexible. All systems have wide-range gauges, but for improved accuracy, capacitance manometers are also available. In case chamber pressure is critical, automatic pressure control is available with control resolutions to 0.1 mbar.
ANNEAL systems are highly modular and can be configured for a wide range of applications.
FEATURES
- Benchtop configuration
- Up to 6” substrate diameters
- Choice of heating technologies up to 1000 °C
- Gas and pressure control
- Base pressures <5 × 10-7 mbar (with TMP)
- Easy sample access
- Define/save multiple process recipes
- Cleanroom compatible
nanoETCH
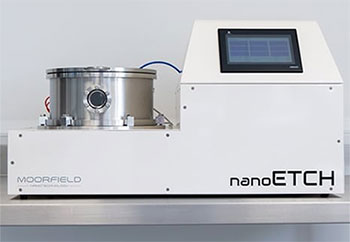
The nanoETCH is a benchtop tool equipped with a high-uniformity plasma etching stage and an RF power supply for plasma generation. The tool was originally developed to provide an etching tool that allowed for precision etching of sensitive 2D materials — not available in conventional RIE tools
Soft Etching is the application of precisely controlled low powers for etching applications involving highly sensitive materials (such as graphene) or where ultra-low etch rates are needed. This allows for the routine use of plasma powers <5 W (down to 100 mW or below, subject to configuration and process), with up to 10 mW control resolution. The nanoETCH has been optimized to provide Soft Etching of carbon nanomaterials, particularly graphene with Ar and/or O2 gases. The optional Fluorinated Process Gas module extends the Soft Etching range to include fine-etch control of harder materials such as 2D materials beyond graphene such as hBN and MoS2 as well as SiO2 and Si.
nanoETCH tools can be fitted with stages for 3"/75mm, 4"/100 mm or 6"/150 mm maximum substrate diameters.